Connecting Rod Manufacturers - The Heart of Diesel Engine Performance
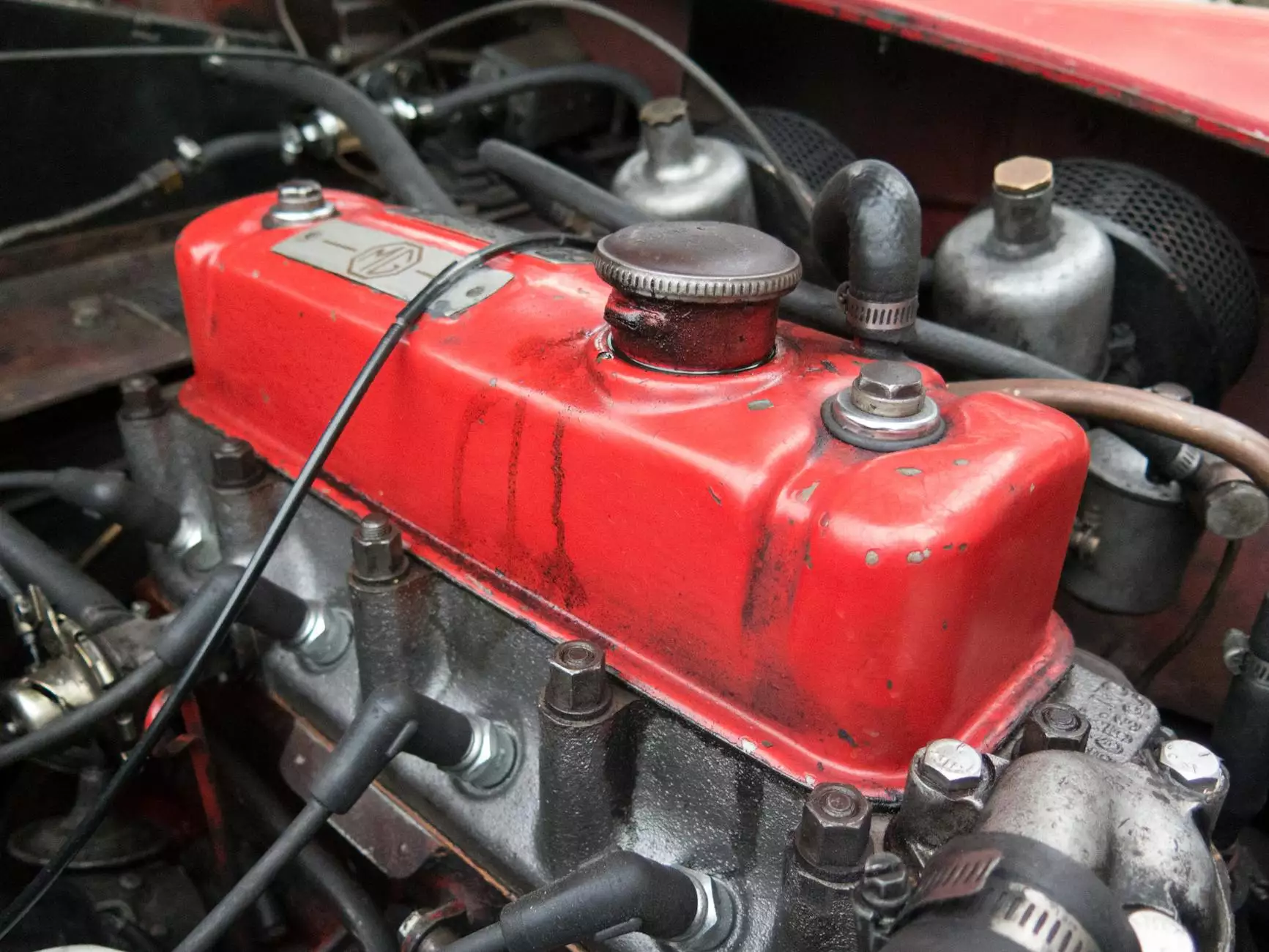
Connecting rods are essential components of diesel engines, acting as the link between the crankshaft and the pistons. As a critical part of the engine's architecture, they play a vital role in converting the linear motion of the piston into the rotational motion of the crankshaft. This article delves deep into the realm of connecting rod manufacturers, exploring their manufacturing processes, the significance of their products, and the future directions for the industry.
The Importance of Connecting Rods in Diesel Engines
Diesel engines are renowned for their durability and efficiency, often employed in a variety of demanding applications including trucks, marine vessels, and industrial machinery. This robust performance largely hinges on high-quality engine components, specifically the connecting rods. Here’s why they are so critical:
- Durability: Connecting rods must withstand immense stresses during operation. They are subject to tensile loads and bending moments that can ultimately affect engine performance and longevity.
- Precision Manufacturing: The quality of connecting rods directly impacts the engine's efficiency and emissions. Precision machining and manufacturing are essential to ensure that each rod meets the stringent requirements of modern diesel engines.
- Weight Reduction: Advanced materials and manufacturing techniques allow for lightweight connecting rods that enhance fuel efficiency without compromising strength.
Types of Connecting Rods Manufactured
Connecting rod manufacturers produce various types designed to meet specific performance requirements and applications. Here are some common types:
1. Standard Connecting Rods
These are widely used in most diesel engines. They are designed to provide a balance of weight, strength, and cost-effectiveness.
2. Performance Connecting Rods
Engineered for high-performance applications, these connecting rods are often made from forged steel or aluminum to improve strength and reduce weight.
3. Custom Connecting Rods
For specialized applications, many manufacturers offer custom solutions. These rods are tailored to meet the unique specifications of an engine, accommodating higher RPMs or specific load requirements.
The Manufacturing Process of Connecting Rods
The process of manufacturing connecting rods is intricate and requires significant expertise, employing advanced technologies. Here’s a simplified overview of the steps involved:
1. Material Selection
The choice of materials is crucial. Most connecting rods are made from forged steel, which provides the necessary strength and durability. Some manufacturers may opt for aluminum alloys to reduce weight.
2. Forging
In this step, the material is heated and shaped into rough rod forms. Forging enhances the material’s grain structure, leading to stronger connecting rods.
3. Machining
After forging, the rough shapes undergo precision machining. This process involves cutting the rods to exact dimensions and creating features such as the wrist pin and crank pin bores.
4. Heat Treatment
To further enhance strength, rods are often subject to heat treatment processes, which relieve stress and improve mechanical properties.
5. Finishing
Finally, the rods are finished with surface treatments such as shot-peening or polishing to improve fatigue resistance and minimize wear.
Quality Assurance in Connecting Rod Manufacturing
Quality assurance is paramount in the manufacturing of connecting rods. Leading connecting rod manufacturers employ rigorous testing protocols to ensure that their products meet industry standards. This includes:
- Dimensional Inspection: Verifying that each rod meets precise dimensional tolerances.
- Fatigue Testing: Assessing the rods under simulated operational loads to ensure durability.
- Material Testing: Conducting tests to evaluate the properties of the materials used, ensuring they are suitable for high-stress applications.
Innovations in Connecting Rod Technology
The landscape of connecting rod manufacturing is constantly evolving. With advancements in technology and materials, the industry is moving towards more innovative solutions. Here are some notable trends:
1. Advanced Materials
Manufacturers are increasingly looking at alternative materials such as titanium and composite materials that offer superior weight-to-strength ratios. These advancements can lead to lighter, more efficient connecting rods.
2. Computer-Aided Design (CAD)
The use of CAD software allows for more precise designs, enabling manufacturers to simulate performance and optimize the geometry of connecting rods before production.
3. Additive Manufacturing (3D Printing)
3D printing technologies are being explored for rapid prototyping and, eventually, for actual production of connecting rods. This method allows for complex geometries and potentially reduced waste.
The Role of Connecting Rod Manufacturers in the Diesel Engine Parts Supply Chain
Connecting rod manufacturers serve a fundamental role in the broader supply chain of diesel engine parts. They are often integral partners for engine builders and automotive manufacturers. Here’s how they fit into the industry:
- Collaboration with Engine Builders: Many manufacturers work closely with engine developers to design connecting rods that meet specific performance criteria.
- Aftermarket Supply: There is a significant market for aftermarket connecting rods, and manufacturers often supply these parts to repair shops and auto parts stores.
- Research and Development: Continual improvements in design and materials are vital. Manufacturers often invest in R&D to stay competitive and innovative.
Challenges Facing Connecting Rod Manufacturers
Despite the advancements and demand for connecting rods, manufacturers face several challenges:
1. Rising Material Costs
The cost of raw materials can fluctuate, impacting production costs. Manufacturers must strategize to manage expenses without sacrificing quality.
2. Competition
With numerous players in the field, staying competitive requires consistently high-quality products and customer service. Companies must differentiate themselves through innovation and branding.
3. Regulatory Compliance
The automotive industry is subject to strict regulations concerning safety and emissions. Ensuring compliance can be a complex and ongoing challenge for manufacturers.
Future Trends in Connecting Rod Manufacturing
Looking forward, the future of connecting rod manufacturing is promising. Key trends to watch include:
1. Sustainability Initiatives
The push for sustainability is leading manufacturers to explore greener processes and materials. Eco-friendly manufacturing practices are becoming a priority.
2. Digital Transformation
Embracing Industry 4.0 principles, manufacturers are utilizing data analytics, IoT, and AI to optimize production and maintenance processes.
3. Global Supply Chain Management
As globalization continues, manufacturers are adjusting their supply chains to be more resilient and adaptable to global events.
Conclusion
In conclusion, connecting rod manufacturers play a crucial role in enhancing the performance, reliability, and efficiency of diesel engines. The continual evolution of manufacturing practices, along with the integration of new technologies and materials, positions the industry for a bright future. By understanding the intricacies of the manufacturing process and the significance of quality assurance, stakeholders can appreciate the vital contribution these manufacturers make to the automotive and industrial sectors.
For further information on high-quality diesel engine parts, you can explore more at client-diesel.com.