Understanding the Significance of 40 Shore in Vacuum Membrane Technology
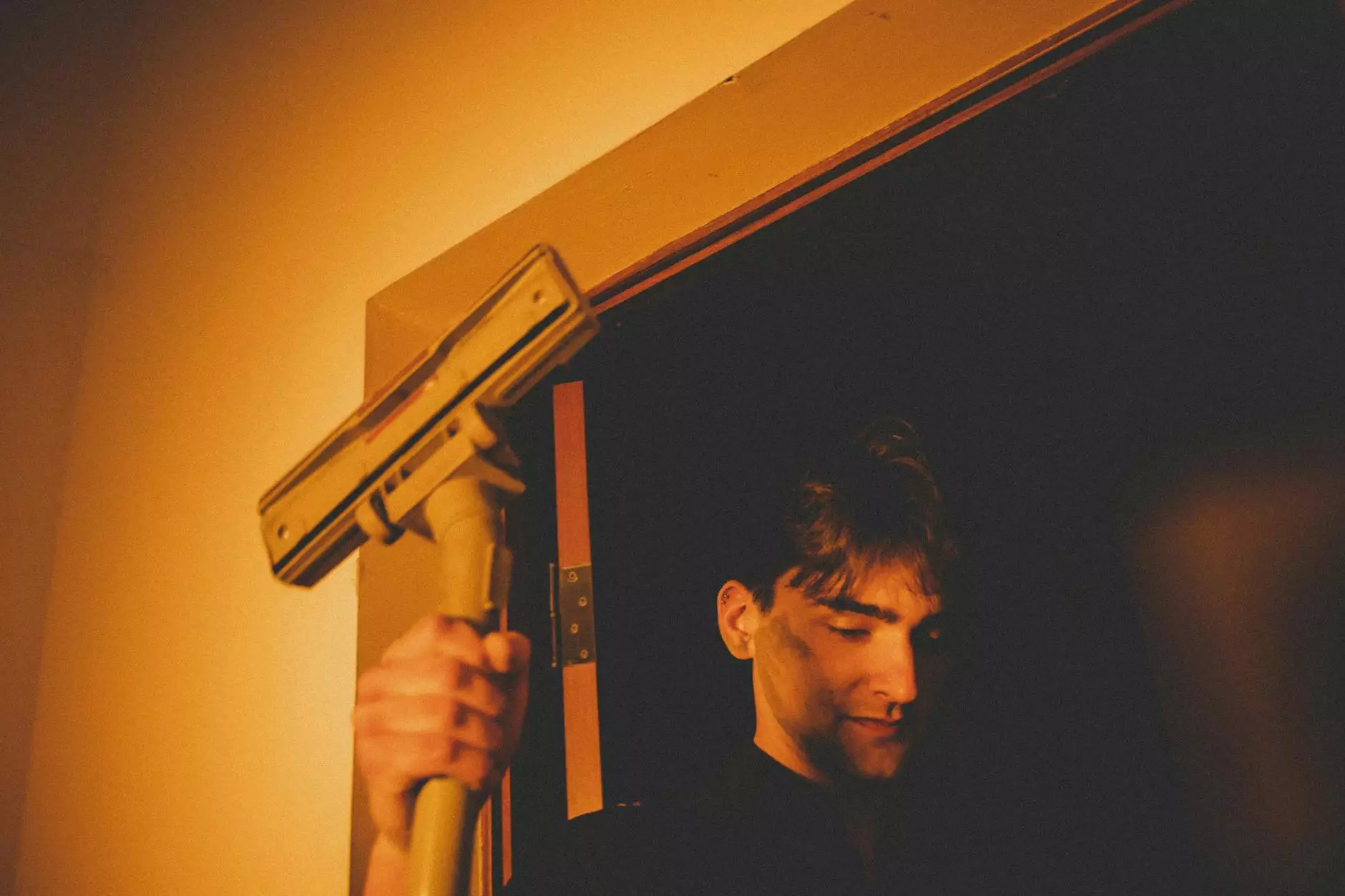
In the realm of vacuum technology, the properties of materials play a pivotal role in the efficiency and effectiveness of equipment. One key aspect that often goes unnoticed is the hardness rating of membranes, specifically the 40 shore hardness. This article delves into the importance of 40 shore hardness in vacuum membranes, exploring its applications, benefits, and the implications for businesses in the industry.
What is Shore Hardness?
Shore hardness is a measure of the hardness of materials, particularly flexible materials like elastomers and polymers. This measurement is crucial in determining how a material will perform under various conditions. The scale traditionally ranges from 0 to 100, with lower numbers indicating softer materials and higher numbers denoting harder ones. The most common scales used are:
- Shore A Scale: Used primarily for softer materials like rubber and flexible polymers.
- Shore D Scale: Utilized for harder materials, typically those that are rigid.
When we refer to a hardness rating of 40 shore, we are specifically discussing a medium-soft material that possesses a good balance between flexibility and strength.
The Role of 40 Shore Hardness in Vacuum Membranes
The application of 40 shore membranes is particularly relevant in the production of vacuum presses and systems that require a high degree of reliability and precision. Here are some key roles that 40 shore membranes play in vacuum technology:
1. Flexibility and Adaptability
One of the standout features of a 40 shore membrane is its flexibility. This property allows the membrane to conform to various shapes and surfaces, facilitating even pressure distribution in vacuum applications.
2. Chemical Resistance
Membranes with a hardness of 40 shore are often formulated to resist a wide range of chemicals. This makes them ideal for industries that involve exposure to various substances, ensuring longevity and consistent performance.
3. Durability Under Stress
The medium softness of 40 shore provides excellent durability under mechanical stress. This ensures that the membrane can withstand the rigors of repeated use without succumbing to wear and tear.
Applications of 40 Shore Membranes
In any discussion about vacuum technology, it’s essential to highlight the varied applications of 40 shore membranes. Their versatility makes them suitable for several industries, including:
1. Manufacturing Industry
In manufacturing, 40 shore membranes are crucial for processes like vacuum forming, where sheets of plastic are heated and formed into desired shapes. The ability to mold around intricate designs is vital for high-quality production.
2. Automotive Sector
Automotive industries often use 40 shore membranes for applications such as vacuum sealing and component fabrication. Their excellent properties ensure that they can withstand the demanding environments found in automotive applications.
3. Aerospace Sector
The aerospace sector benefits from the lightweight yet sturdy nature of 40 shore membranes, making them ideal for components requiring both strength and flexibility under varying atmospheric pressures.
4. Electronics
In electronics manufacturing, these membranes are used in creating vacuum-sealed packages that protect sensitive electronic components from moisture and contaminants, showcasing their critical role in the integrity of electronic devices.
Choosing the Right Membrane: Factors to Consider
When selecting membranes, especially those rated at 40 shore, there are several factors that businesses must consider:
- Temperature Resistance: Ensure the membrane can withstand the operational temperature without degrading.
- Thickness: The thickness can significantly affect the performance; choose according to the specific application needs.
- Material Composition: Different materials possess different properties, affecting the overall performance and suitability for specific applications.
- Supplier Reputation: It is crucial to source membranes from reputable suppliers to ensure quality and reliability.
Benefits of Using 40 Shore Rubber and Silicone Membranes
The choice between rubber and silicone membranes, both of which can be formulated to achieve a 40 shore hardness, can significantly affect the outcome of your applications. Here are the benefits of both types:
40 Shore Rubber Membranes
Rubber membranes provide excellent elasticity and durability. They are often favored for their abrasion resistance and ability to handle dynamic applications, which makes them ideal for manufacturing processes that involve frequent movement or pressure.
40 Shore Silicone Membranes
Silicone membranes generally offer superior thermal stability and resistance to harsh chemicals. They are often used in applications requiring high temperatures or exposure to aggressive substances, making them invaluable in many industrial settings.
The Future of 40 Shore Membranes in Vacuum Systems
As technology evolves, the materials used in vacuum systems, especially those with a 40 shore rating, are expected to advance. Innovations in polymer science are leading to the development of more effective and adaptable membranes that can meet the increasing demands of various industries.
1. Enhanced Performance Through Innovation
With ongoing research, manufacturers are likely to introduce membranes that offer improved performance characteristics such as enhanced strength, better chemical resistance, and extended operational life. Advances in production techniques could also lead to cost-effective solutions without compromising on quality.
2. Eco-Friendly Developments
The industry is gradually moving towards eco-friendly materials that retain the beneficial properties of traditional membranes while being more sustainable. This shift is crucial as businesses worldwide adopt more environmentally conscious practices.
3. Customization and Specialization
With the demand for tailored solutions increasing, suppliers of 40 shore membranes will likely focus on providing specialized products that cater to specific applications in a variety of sectors, enhancing usability and effectiveness.
Conclusion
Understanding the significance of 40 shore hardness in vacuum membranes is critical for businesses operating in various industries. From buying membranes to incorporating silicone and rubber membranes into production lines, recognizing the unique properties and applications can lead to improved efficiency, cost savings, and enhanced product quality. As the demand for reliable and high-quality vacuum systems continues to grow, the importance of choosing the right membrane cannot be overstated. With ongoing developments and innovations, the future of 40 shore membranes looks promising, making it a key factor for success in the vacuum presses industry.